AOI: Commercial Space in Low Earth Orbit
Innovation:
The proposed work will focus on the understanding and quantification of the challenges associated with materials joining in space conditions. This work includes developing and using an autonomous welding system that reproduces the vacuum, temperature, and gravity conditions encountered during manufacturing, maintenance, and repair in space.
This work will advance the technology readiness level (TRL) of laser beam welding (LBW) of metals and ultrasonic welding (UW) of thermoplastics and advanced composites under space conditions from a TRL 3 to TRL 5. An autonomous welding system will be implemented using a vacuum chamber currently under development by a multidisciplinary undergraduate Capstone team at The Ohio State University (OSU), which is co-sponsored by NASA and OSU. This unique facility will consist of a vacuum chamber integrated with heating/cooling systems, motion devices, controls, and a sensor array, which will enable LBW and UW operations. This system is designed for materials joining under space conditions, including LEO, Moon, and Mars gravity (via parabolic flights), extreme temperatures, and vacuum. As data collection is a critical component of the proposed work, a sensor array is integrated with the chamber to maximize the data gathered during welding. This data will be used for future modeling efforts that will reduce experimental costs and accelerate and de-risk technology development.
An understanding of the application of welding in space needs to be developed, and this project will build such for both LBW and UW. These processes have been identified by our industry and government partners as the most versatile options for welding-based fabrication and repair in space. The stated work plan for the LBW and UW tests will utilize a scientific approach to optimize process parameters for high performance alloys, polymers, and composites used in aerospace applications. The objective of this work is to construct a comprehensive database of known performance metrics in “On Earth” and “Low Earth Orbit” environments.
The LBW work will provide critical data on the effects of extreme space conditions, including temperature, gravity, and vacuum, during laser welding of aluminum, and stainless-steel alloys. The sensor array in the chamber will enable detailed process monitoring during terrestrial and parabolic flight tests. The LBW of metals in space work will involve differentiated gravity and temperatures, as well as a vacuum environment, which will require a combination of laboratory and parabolic flight work.
Agile Ultrasonics (AU-LLC) has developed a novel approach for UW of high-performance thermoplastics and carbon-reinforced thermoplastic composites. This innovative approach has demonstrated the ability to generate high-strength welds without using energy directors, implanted heat generation devices, insert films, or other enhancement devices, making it suitable for welding in space.
As UW is a solid-state process, differentiated gravity plays a less relevant role, and therefore UW of polymers and composites will only involve differentiated temperatures and vacuum, which can all be performed at the laboratory at AU-LCC and OSU. Data from this work will significantly increase the knowledge base of the effects of varying temperatures and vacuum on ultrasonic plastic welding. AU-LLC will deploy the technology and knowledge base to commercial and government aerospace agencies through a modular set of ultrasonic tooling systems. UW is an extremely fast, low-energy consumption technology that has demonstrated significant advantages by way of reduced process forces and reduced need for heavy support tooling systems. Efforts from this work will be demonstrated on robot and/or multi-axis automation systems capable of operating in “Low Earth Orbit.” Outcomes will be immediately applicable to aero, auto, EV, and consumer markets through Agile’s commercialization strategy. The autonomous welding instrumentation and welding in space conditions testing will directly impact the future space missions of Nanoracks, NASA, and the AFRL, as well as the technology and business development of our terrestrial partners Agile Ultrasonics, IPG Photonics, and the Lincoln Electric Company. The autonomous welding system will be a prototype for future automated systems to be deployed in space missions. The data gathered throughout testing is critical to all future welding-based in-space manufacturing, maintenance, and repair.
Objective:
Development of Autonomous Metals and Polymer Welding Technology for Space Applications. From the understanding of fundamental challenges to the construction of a prototype to support future R&D for the In-Space, Servicing, Assembly, and Manufacturing (ISAM) sector.
Background:
The first and last American space welding mission occurred on the Skylab in 1973. The fast-growing In- Space, Servicing, Assembly, and Manufacturing (ISAM) sector lacks an understanding of the basic application of welding in space because there has been no work in this area. The NASA and AFRL partners recognize that the current lack of understanding of space welding requires initial efforts to be focused on the development of basic capabilities, which can then be exploited in future projects for their exploration and defense missions as well as industrial commercialization.
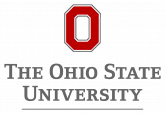
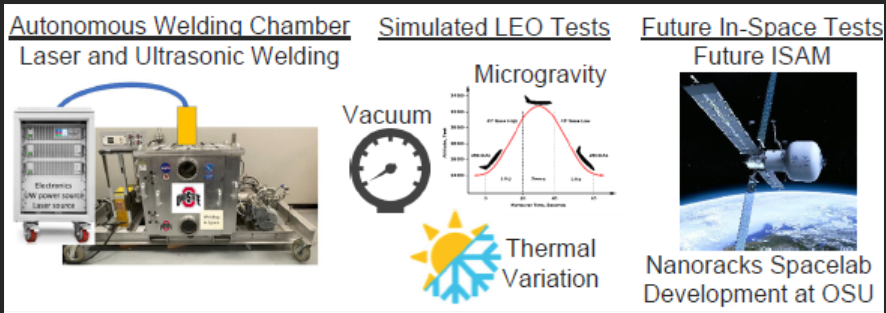